Technological Innovations and Quality Control Processes in Aluminum Production
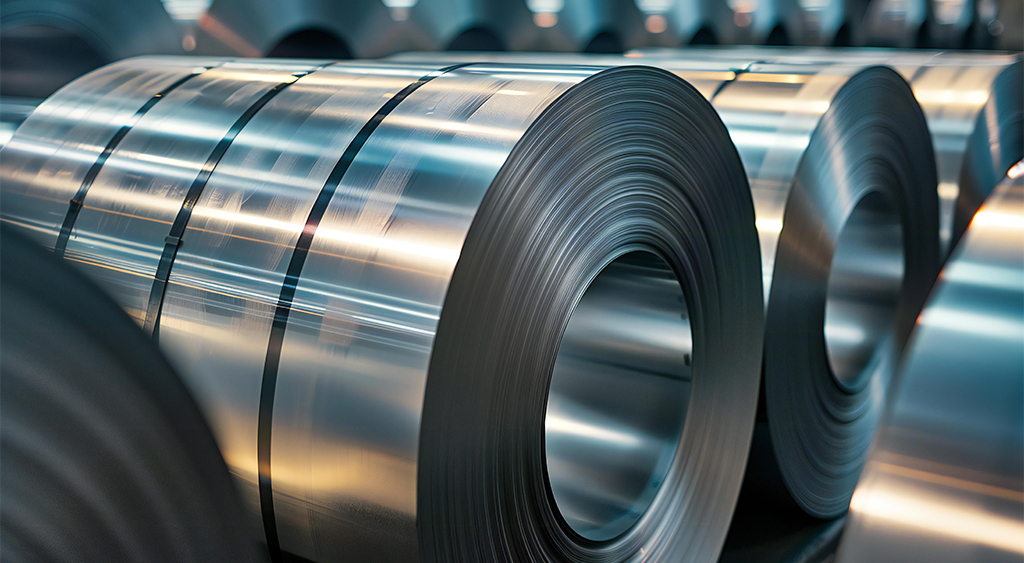
Technological Innovations and Quality Control Processes in Aluminum Production
Aluminum, with its lightweight structure, durability, and resistance to corrosion, stands as a backbone of modern industry. Its extensive applications span from automotive to construction, aerospace to packaging, making this valuable material increasingly significant in today’s world. Understanding the innovations necessary to enhance the efficiency and quality of aluminum production is crucial in contemporary industry. In this article, we will explore the latest technological developments in aluminum production and the control mechanisms used to ensure quality throughout these processes.
The Aluminum Production Process
Aluminum is primarily derived from bauxite ores. Initially, these minerals are converted into aluminum oxide (alumina) through the Bayer process. Subsequently, the Hall-Héroult process reduces alumina into metallic aluminum. This two-step production process has been enriched by numerous innovations in recent years.
1. Energy Efficiency
Aluminum production is notoriously energy-intensive. Therefore, innovations aimed at increasing energy efficiency have gained paramount importance. Modern electric melting furnaces have the capability to produce more aluminum while consuming less energy, making them stand out in the industry. Additionally, innovative electric systems and energy recovery technologies have not only made production processes more sustainable but have also significantly reduced costs.
2. Waste Management and Recycling
Waste management remains one of the major challenges faced by aluminum production. However, recent advancements in recycling technologies have enhanced the reusability of aluminum. For instance, advanced sorting and cleaning techniques employed in modern recycling facilities have increased recycling rates while substantially decreasing energy consumption. This development contributes significantly to minimizing environmental impacts.
3. Advanced Material Technologies
New alloy designs and innovations in materials engineering have considerably improved the performance of aluminum. Particularly, aluminum alloys produced using nanotechnology are setting new standards in both durability and lightweight characteristics. Such advancements hold revolutionary potential, especially in the aerospace and automotive sectors.
Quality Control Processes
In aluminum production, quality control plays a vital role in ensuring the reliability and performance of final products. Quality control processes must be meticulously implemented at every stage of production.
1. Raw Material Control
The quality of bauxite and other raw materials used in aluminum production directly influences the quality of the final product. Thus, strict quality control processes during raw material procurement are essential. Laboratory tests and chemical analyses serve as critical tools for assessing raw material quality. At every stage, the presence of unwanted residues and components must be carefully monitored.
2. Process Control
Throughout the production process, continuous monitoring of critical parameters such as temperature, pressure, and chemical composition is essential. Automated control systems used in modern facilities track these parameters in real time, minimizing deviations. This approach not only reduces production errors but also safeguards product quality.
3. Final Product Control
Quality control of final products is conducted through mechanical tests, chemical analyses, and visual inspections. In particular, strength tests and corrosion resistance tests of aluminum alloys are crucial for ensuring product reliability. Furthermore, certification processes are carefully implemented to ensure compliance with international standards.
4. Monitoring and Feedback
Another key component of the quality control process is continuous monitoring and feedback mechanisms. Any errors or anomalies that arise during the production process can be swiftly detected and rectified. This approach not only enhances production efficiency but also secures the quality of the final product..
Future Directions
Technological innovations and quality control processes in aluminum production are in a constant state of evolution. Looking ahead, the integration of cutting-edge technologies such as artificial intelligence and machine learning is likely to further optimize production processes. These advancements promise to lower production costs while also reducing environmental impacts.